
Case Study
“We have used Magnalube for the same applications since 1985”
Two of the main product lines that Wadsworth manufactures are energy curtains and vent automation systems. Their Powerpull Energy Curtains provide easy, automatic shading to greenhouses that allow growers to control the internal temperatures by reducing the amount of sunlight and humidity. Their vent automation systems regulate the amount of heat and condensation present in greenhouses by automatically opening and closing vents.
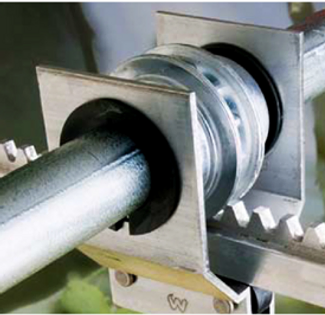
Variable temperatures, moisture, extended service life and compatibility with plastic parts are all key design challenges that Wadsworth faced when selecting a proper lubricant. Oils and lower quality greases tend to evaporate and migrate when used in applications that are exposed to elevated temperatures and high humidity. Conventional lithium greases, especially in the presence of moisture, will soften and bleed, causing the grease to break down and migrate away from critical areas. In addition, solvent refined base oils are common in cheaper greases and can cause damage to plastic parts over time. With all of these challenges to balance, Wadsworth was required to look comprehensively at lubrication options for optimal design performance. The lubrication criteria to maximize equipment reliability were: excellent adhesion, corrosion protection, high quality base oils and the longevity of the product.
“We needed a lubricant that was resilient enough to hold up to high temperatures and humidity…”
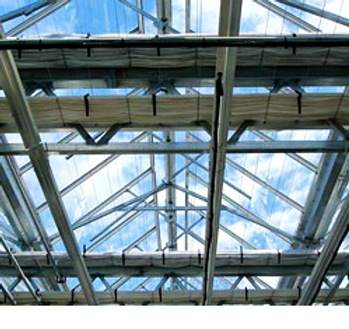
In the end, Wadsworth Control’s comprehensive approach to product design paid off because they found a lubricant that stood the test of time. “We have used Magnalube for the same applications since 1985,” attests Williams. “We send a can with every shade system, and then the various greenhouses can reapply it if needed.” Williams continued, “they very seldom need another can, so it lasts a very long time.”
Get In Touch
If you have any questions, comments, or concerns about our Magnalube greases, feel free to leave us a message.
We will do our best to reply back as soon as possible.